Home Inspection Report Addendum
At CNHInspections, our goal is for your report to be succinct enough that it is easy to navigate. We also strive to provide you with invaluable information included with your report regarding defects, systems & components of the home, limitations and more, as sharing knowledge and providing more information is the basis of our company. E.g., if 'open grounds' are present in the home's electrical system, we want to inform you on what this is and why it is a hazard. If the home has a heat pump or say a sewage ejector pump, we desire to inform you on what these systems in the home are and how they work.
Throughout your report in both the information header sections and in the defect comments it reads, ‘For more information from CNHInspections please click HERE’ which links you to sections of this page, as each section in the following Table of Contents has its own URL link to direct you quickly to the applicable information.
In this report addendum you have exclusive access to invaluable information, illustration photos, code check photos and external links to blogs & videos. Enjoy!
TABLE OF CONTENTS
-
Shingles: Architectural/Laminated Shingle
-
Gutters 101
-
Garage Door Safety: Resistance Not Tested
-
Garage Separation: Garage Area to Living Space Separation Information
-
Attic Ventilation: Information
-
Attic - Mixed Ventilation Methods
-
Exhaust Fan - Not Terminating to the Exterior
-
GFCI: Information
-
Reinspection Information
-
CSM's Present - Limitations
-
Aged Panel and/or Wiring
-
Neutrals - Sharing Terminal
-
Knob and Tube: Information
-
Wiring - Braided Cloth NM Present
-
Two-Prong Present
-
Open Ground (Older Wiring)
-
Open Ground (GFCI Protected)
-
Open Neutral
-
Interior Unit (Gas) - Aged
-
Lateral Load Devices - Missing
-
More coming soon...
Shingles: Architectural/Laminated Shingle
The roof covering was comprised of architectural composition shingles. Architectural shingles, also called dimensional shingles, are thicker and heavier (often 50% more) than traditional 3-tab shingles. These "premium" shingles are manufactured by starting with a fiberglass reinforcement mat, multiple layers of asphalt are added over the mat, and lastly, granules coated with ceramic are added over the upper layer of asphalt for protection against the elements (wind, rain, and UV rays from the sun). Architectural shingles typically have higher wind resistance numbers, resist leaks better, and have a longer warranty than their 3-tab counterparts.
Due to the many variables which affect the lifespan of roof covering materials, the remaining service life of any roof coverings is not estimated. This is in accordance with all industry Home inspection Standards of Practice. The following factors can affect the lifespan of roof covering materials:
-
Roofing material quality: Higher quality materials will, of course, last longer.
-
The number of layers: Shingles installed over existing shingles will have a shorter lifespan.
-
Structure orientation: Southern-facing roofs will have shorter lifespans.
-
Pitch of the roof: Shingles will age faster on a lower-pitched roof in comparison with higher pitches.
-
Climate: Wind, rain, and snow will impact the lifespan of the roof.
-
Color: Shingles that are darker in color will have a shorter lifespan than lighter-colored shingles.
-
Attic Ventilation: Poorly vented attic spaces will decrease shingle life due to heat.
-
Vegetation Conditions: Overhanging trees, branches, contacting the roof, or leaf cover drastically shorten lifespan.
Asphalt shingles must be installed per manufacturers' recommendations to uphold warranty coverage. These installation requirements vary widely from manufacturer to manufacturer and across the multitude of different shingle styles manufactured. An inspection of the roof covering material will be conducted to the best of my ability, but confirming proper fastening, use and adequacy of underlayment, and adequacy of flashing is impossible as these items are not visible and are far beyond the scope of a visual only inspection. Damaging and invasive means would have to be carried out to confirm proper installation. Therefore, the inspection of the roof is limited to visual portions only.
Gutters 101
KICKOUT FLASHING MISSING OR IMPROPER: Kick-out flashing prevents moisture intrusion by directing rain water into the gutter and preventing it from getting behind the siding. Typically, a kick-out flashing is 6" in height (some manufactures allow for 4") and "kick into" the gutter at a 110-130 degree angle. For more information, please read the InterNACHI article regarding 'Kick-out Flashing' HERE. Also please click HERE for even more information.
DOWNSPOUT(S) EXTENSIONS IMPROPER/MISSING: Current standards require downspouts to be diverted at least 4ft from the foundation of the home to prevent the grounds surrounding the foundation from becoming saturated. Saturated grounds can allow water/moisture to enter basement and crawl space areas, and in extreme cases, can allow for settlement of the home. In slab foundations, saturated grounds can lead to undermining of the soil supporting the structure which can subsequently cause damage and/or cracking to the slab foundation. Properly extending all downspouts at least 4ft away from the home is recommended.
FYI: They may need to extend much further depending on your soil, if the house is located on a sloped hillside, and local buildings codes etc…
DOWNSPOUT TERMINATING ON HARDSCAPE: This can create a fall hazard in freezing temperatures due to the water that comes from the downspout freezing. Repairs or modifications are recommended to divert the downspouts to an area that will not create a fall hazard.
DOWNSPOUT TERMINATING NEAR DECK FOOTING: Downspouts dumping water near deck footings will concentrate water against them and greatly increase the potential for problems with settled footings or frost heave. Add solid aluminum downspout extensions to carry the water at least 4ft away from the footings.
SPLASH BLOCKS: While better than the downspouts terminating directly at the foundation, splash blocks do not meet today's standards for diverting rainwater 4ft away from the foundation. The installation of proper downspout extensions or drain tubes to carry rainwater at least 4ft away from the structure is recommended.
GUTTER AND/OR DOWNSPOUTS TERMINATING ON ROOF: Shingle manufacturers will not cover damage to the shingles caused by guttering discharging water onto the roof surface. This discharged water can loosen the ceramic granules and cause premature aging of the shingle surface. Please see the photo below of a technical bulletin from GAF addressing this. The downspouts are recommended to be routed to discharge into the lower guttering.
DOWNSPOUT INADEQUATE CONNECTION: An inadequate connection to a drain tube or extension can allow water to saturate the grounds in the area of the downspout, possibly adding moisture to adjacent interior areas. A proper connection or repairs as needed preventing the possibility of any water spillage is recommended.
MISSING, LOOSE, DAMAGED, MISALIGNED DOWNSPOUTS: This can result in excessive moisture in the soil at the foundation, which can lead to foundation/structural movement. Repairs are recommended.
DAMAGED, LOOSE AND/OR CORRODED GUTTERS: This could allow water intrusion onto the adjacent siding and facilitate deterioration and/or ponding near the foundation. This can also result in excessive moisture in the soil at the foundation, which can lead to foundation/structural movement. Repairs/replacement is recommended.
GUTTERS IMPROPER SLOPE: Standing water and organic debris present in the gutters can be due to clogged downspouts and/or an improper pitch of the gutters. This puts strain on the gutter fasteners, and may allow water to overflow the guttering, possibly damaging fascia and saturating the grounds preceding the foundation walls. Repairs are recommended to achieve proper drainage of the guttering system.
INDICATION OF LEAKS: Indications of past or present gutter leaks may include moisture staining, mildew at gutter joints, soffit areas, and/or fascia boards etc. An evaluation of any such areas is recommended with repairs made as needed to ensure no further leaking occurs. Any related damage should be repaired at this time as well.
FYI: Leaking gutters cannot be diagnosed if an active rain was not occurring at the time of inspection.
DEBRIS: Leaves/debris and/or ceramic granules are recommended to be removed to prevent blockages in the downspouts, as blockages will allow water to overflow the gutters.
MISSING FASTENERS/SPIKES BACKED OUT: Missing gutter fasteners or backed out spikes can allow the guttering to sag, allow for leaks, and may allow for the guttering to become detached if they were to fill up with water. Repairs to properly secure the guttering is recommended.
MISSING ENDCAP: This will allow rainwater to flow out of the end of the gutter. The installation of an endcap is recommended.
GUTTERS OVER DRIP EDGE: Gutters installed over the drip edge flashing instead of behind it can allow rainwater to infiltrate between the gutters and fascia of the home due to water tension. Repairs to install the gutters behind the drip edge flashing is recommended. For more information please click HERE.
VINYL GUTTERS: PVC (Vinyl) gutters are very inexpensive in comparison with aluminum guttering. They are prone to crack, leak, and warp as they age and are exposed to the elements. Replacement of the gutters with a permanent solution should be expected in the near future.
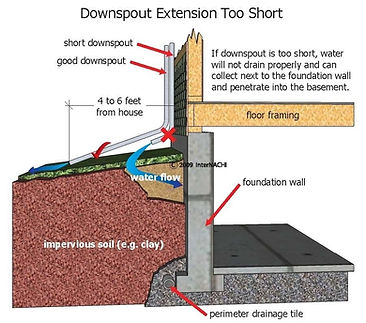





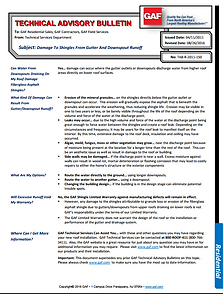
Garage Door Safety: Resistance Not Tested
EXCL - The "Resistance" test of the garage door(s) was not conducted due to the possibility of damaging the door and/or the opener should the resistance feature not function properly. This functionality is excluded from this inspection. Garage doors contain two safety measures to prevent someone from being injured or pinned by a closing garage door: Photoelectric eyes and the ability to auto-reverse if the door meets resistance or a solid object. I recommend testing this feature for functionality once taking ownership of the home. The test can be conducted by placing a 2" X 4" laid on the ground underneath the door. When the door is closed, it should contact the 2" X 4" and auto-reverse. If it does not, adjustments to the "force close" setting on the opener may need to be made, and/or a garage door contractor should evaluate. Be advised, however, that testing this safety feature may result in damage to the door, opener, or both, which is why this test is not conducted at the time of inspection. For a short video showing how to perform a "resistance test", please click HERE.
Garage Separation: Garage Area to Living Space Separation Information
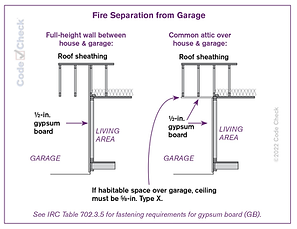


Current building standards for homes require garage to living space separation. This separation helps to slow a garage-originated fire and helps prevent CO gases from entering living areas. Deficiencies to the fire separation are recommended to be upgraded for safety, and a qualified contractor can be consulted for more information. Additionally, any gap in a garage fire separation wall should be sealed, regardless of size, as even small openings can allow smoke and flames to spread from the garage to the living space. Sealing the area(s) with fire-resistant caulk or other approved materials to maintain the integrity of the fire barrier is recommended.
Garage to living space separation is achieved by the following:
DOOR: The interior door leading from the garage into the home must meet the following garage separation requirements:
2006 International Residential Code (IRC) R309.1 Openings from a private garage directly into a room used for sleeping purposes shall not be permitted. Other openings between the garage and the residence shall be equipped with solid wood doors not less than 1-3/8” in thickness, solid or honeycomb-core steel doors not less than 1-3/8” thick, or 20-minute fire-rated doors.
Additionally, doors leading to living areas should have tight seals around their joints to prevent seepage of fumes into the living areas of the house. If doors have windows, the glass should be fire-rated. Pet doors violate the integrity of a fire barrier and should not be installed in fire-rated doors. Doors should be self-closing. Any spring-loaded hinge that needs adjusted to allow the door to self-close can be done so by the following instructions HERE.
WALL & CEILINGS: 2006 International Residential Code (IRC) R309.2 The garage shall be separated from the residence and its attic area by not less than 1/2-inch gypsum board applied to the garage side. Garages beneath habitable rooms shall be separated from all habitable rooms above by not less than 5/8-inch Type X gypsum board or equivalent. Where the separation is a floor-ceiling assembly, the structure supporting the separation shall also be protected by not less than 1/2-inch gypsum board or equivalent. Garages located less than 3 feet from a dwelling unit on the same lot shall be protected with not less than 1/2–inch gypsum board applied to the interior side of exterior walls that are within this area.
The garage firewall should extend from the floor to the roof, however if the ceiling material is fire-rated, the firewall can terminate at the ceiling. Additionally, drywall joints shall be taped or sealed, and holes and/or protrusions through the separation walls should be sealed.
ATTIC COVERS: Attic covers should be made from an approved, fire-rated material, plywood is not permitted. Drywall edges on both the cover and the surrounding area exposed to physical damage should be protected.
VENTS & DUCTWORK: Dryer exhaust ducts should not penetrate garage walls, as they are generally made from plastic and will easily melt during a fire. HVAC ducts should meet the following requirements: 2006 International Residential Code (IRC) R309.1.1 Ducts in the garage and ducts penetrating the walls or ceilings separating the dwelling from the garage shall be constructed of a minimum No. 26-gauge steel sheet or other approved material, and shall have no openings in the garage.
For more information please see the InterNACHI article 'Attached Garage Fire Containment'.
Attic Ventilation: Information
The attic ventilation was reported on by a visual inspection of the above-designated ventilation sources and looking for indications of improper ventilation. Measurements of ventilation sources are beyond the scope of a home inspection and were not conducted. No indications of inadequate ventilation were observed at the time of inspection unless otherwise noted in this report.
Attic ventilation is a frequently-misunderstood element of residential construction. All roof cavities are required to have ventilation. The general default standard is one sq ft of ventilation for every 150 sq ft of attic area, and ideally, this comes from at least 60% lower roof cavity ventilation and 40% upper. The most important elements for healthy attic spaces are:
-
Make sure the ceiling between the living space and the attic is airtight.
-
Ventilate consistently across the whole lower part of the roof cavity with low intake soffit venting.
-
Upper roof cavity venting is less important and if over-installed, can exacerbate heat loss into the attic from the living space.
-
Avoid power ventilators which can depressurize the attic and exacerbate air migration from the house into the attic.
For more information, please click HERE.


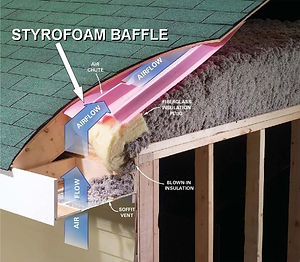
Attic - Mixed Ventilation Methods
Multiple methods of ventilation may conflict with each other and not allow proper cross ventilation. Inefficient airflow not only can damage the roof deck but it can also reduce the lifespan of asphalt shingles. In order for cross ventilation to occur and to properly ventilate the attic, air should flow into the attic near the lower portion of the attic. Air should exhaust out of the upper portion of the attic. With the current ventilation methods on the roof, air is likely not going to flow in and out as it should, and having mixed ventilation methods can short-circuit the airflow pattern in the attic space. Attics with mixed ventilation methods should be evaluated and corrected as necessary.
For additional information please click HERE to watch a short video, or HERE to read an article from roofing magazine.
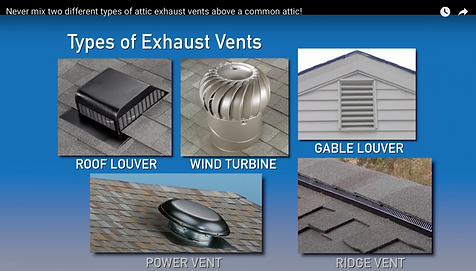

Exhaust Fan - Not Terminating to the Exterior
Exhaust air should not be exhausted into an attic, soffit, roof vent, crawlspace, or other areas inside the building. Exhaust vents terminating into the building can cause condensation, mold and/or moisture damage. Also exhaust fans should not have a soffit termination point within the "passive soffit zone". Though acceptable in some cities, this is not recommended and prohibited by current standards as soffit vents are inlet vents, and the warm, moist air can be directed back into the structure. There are certain types of soffit exhaust termination vents that are acceptable such as the "PreVent-It 4-inch under-eave soffit vent". According to Texas A&M University this vent displaces 95%+ of exhausted air away from the "passive soffit zone". Improper exhaust vent termination points are recommended to be relocated or upgraded for optimal performance.
For more information please see, 'Inspecting the Bathroom Exhaust Fan' by InterNACHI.
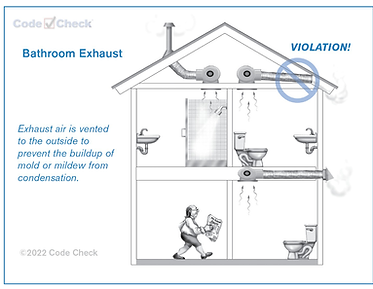
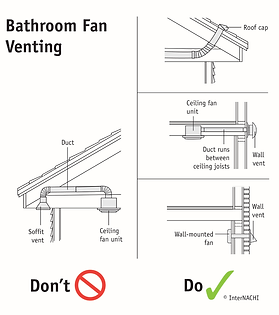

GFCI: Information
LMT - GFCI protection is only tested for if the circuit is protected by a visible receptacle containing a "Test" and "Reset" button, or a GFCI/AFCI breaker in the electrical panel. Underwriters laboratory only recognizes testing this protection by depressing the "Test" button on the receptacle or breaker and not by the use of a polarity tester. Additionally, testing GFCI's with a polarity tester can trip a GFCI receptacle (containing a test/reset button) that is not accessible and/or not visible (often times they are hidden by personal belongings) which then leaves multiple receptacles in the entire circuit inoperable. In accordance with the standards of practice, GFCI receptacles (containing a test/reset button) and/or GFCI breakers are tested as they are found, and to determine where GFCI's should be located is beyond the scope of a home inspection. Please see the illustrations below where GFCI-protection is recommended to be installed. For more information please click HERE.
1) Ground Fault Circuit Interrupter (GFCI) is a protection feature that allows a circuit or receptacle to "trip" or "shut off" if as little as a 5 milliamp differential is detected between the "hot" and "neutral" conductors. Although GFCI protection may not have been required in some or all of these areas when the home was built, their installation is highly recommended and is typically inexpensive.
Therefore, in accordance with the standards of practice, GFCI receptacles (containing a test/reset button) and/or GFCI breakers are tested as they are found, and to determine where GFCI's should be located is beyond the scope of a home inspection.
(6) General Exclusions.
(a) Home inspectors are not required to report on:
5. Compliance or non-compliance with adopted codes, ordinances, statutes, regulatory requirements or restrictions;
GFCI is recommended to be present on the exterior of the home, on kitchen countertops and islands, in bathrooms, laundry rooms, garages, unfinished basements and crawl spaces, and any other area(s) within 6' of a sink's edge. Any comments in the report regarding missing GFCI's are given as a courtesy and is not an all inclusive listing of any missing GFCI's.

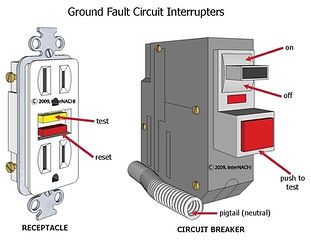

Reinspection Information
It is HIGHLY recommended that licensed professionals are used for repairs or replacement of deficiencies referenced in this report, and that copies of their receipts/invoices are provided to you for verification and warranty purposes. CNHInspections does not perform re-inspections or verifications of any repairs performed after the home inspection, as doing this typically involves confirming the adequacy of a repair. The reason for this is that a home inspector has a general knowledge in ALL areas of a home, a contractor such as an electrician, a plumber etc... is an "expert" and specializes in their specific field of expertise. Home inspectors typically have the knowledge to know when a system or component in a home needs further evaluation and/or repair, and contractors have the knowledge on how to carry out that repair. For this reason we refer you to these experts who are "specialists" in their specific field of work to perform further evaluations/repairs. If you have concerns of any repairs being done, we recommend that verifications/re-inspections be performed by a licensed third party contractor related to the applicable work being performed e.g., an electrician, who is an expert in their related field to verify that the repairs were made according to today’s industry standards. It is also very important that you verify that the necessary permits were pulled and closed to ensure any contractors who worked on the property had the required licenses. Typically the seller(s) have copies of invoices, inspections, permits, etc., for warranty, liability, and tax purposes. It is highly recommended to ask the sellers for any of this information.
CSM's Present - Limitations
IMPORTANT - PLEASE READ - When reading this report you will see that some degree of movement, or interior and/or exterior wall crack(s) were found at this property, and they are reported on by their presence and visual condition as existing at the time of inspection only. I cannot render a professional opinion as to a crack's severity, cause, or whether it has been recently active. Only a Structural Engineer can render a judgment on a crack's severity, cause, and repercussions and they should be consulted as desired. Furthermore, a crack within normal tolerances may have been in the same condition for many years with no activity, or it may be newly formed and still active. I recommend consulting with the seller(s) about the history, including recent activity, of any cracking that is present. Therefore, if you would like ANY referenced cracks evaluated, quoted, or repaired, a foundation contractor or other qualified tradespeople should be consulted prior to the end of your inspection contingency period.
Cracks can be present on brick veneer, foundation walls, drywall in the home, etc. I typically find some degree of cracking on over 50% of the homes I inspect, and ALL cracks initially start as a small crack, which is another reason I can not render an opinion on the severity of a crack.
Several conditions can lead to the formation of cracking.
-
Typical cracking can occur in the first five years after a home is constructed as the soil is considered "disturbed earth". The weight of the structure will bear on this graded/disturbed soil, and the soil will compact allowing for "settlement" or movement of the home. After approximately five years the soil is once again considered "undisturbed earth", and the majority of the settlement has taken place. Some settlement can still occur after this five-year period, but typically not to the degree that occurred in the first five years.
-
Other conditions and deficiencies can also allow for settlement or movement, including but not limited to; excessive rain, drought conditions, improper grading surrounding the structure, inadequate footer drains, the composition of the soil, the floor structure design, etc. Cracks or movement associated with these conditions typically will require some degree of repairs.
I look for several conditions in association with cracks on foundation walls or veneers, and if any of these conditions are observed, the crack will be described as being outside of normal tolerances, and further evaluation will be recommended;
(1.) Lateral Displacement - When you rub your hand over the crack is one side of the wall jutted out in comparison with the other side.
(2.) The width of the crack's "gap" - Typically any crack over 1/4" in width should be evaluated.
(3.) A tapering gap - A crack that starts out over 1/4" in width and tapers to a hairline crack may show differential settlement.
(4.) The number of cracks - If there are several cracks that are all within normal tolerances, it's the culmination of all the cracks that is important.
(5.) Multiple cracks on drywall/plaster - Multiple cracks over window and door opening or on ceilings may be associated with settlement, thermal expansion, expansion/contraction of differing building materials, etc.
(6.) Visible settlement associated with the crack - When the mortar line is followed across a crack, if a "drop" is observed with brick or block, evaluation will be needed.
Aged Panel Information
Electrical panels and wiring are one of the most important components in the home. According to Underwriters Association of America any panels over 30 years of age are recommended to be evaluated by a licensed electrician. (An electrician will be able to be invasive with their inspection, and may find deficiencies that were not seen during a "visual-only" home inspection) to ensure they are performing as intended. Panelboards 40 or more years old should also be upgraded/changed out at your earliest convenience. Panels manufactured in recent years are inherently safer due to more rigorous testing, safety features, etc.
For more information, please click HERE. Also, a typical life expectancy chart from CNHInspections can be found HERE.
Aged Wiring Information
Electrical wiring is just like any other item, and has a certain life span (50-70 years is typical) and replacement of aged wiring should be anticipated. While receptacles and switches are readily accessible and easily replaced when broken, the electrical wiring remains unseen and untouched. Electrical wiring and wire insulation will deteriorate over time and can become cracked, brittle, or covered with oxidation that can cause circuits to overheat. For more information, please click HERE. An electrician should be consulted to learn of future repair or replacement costs of aged wiring (an electrician will be able to be invasive with their inspection, and may find deficiencies that were not seen during a "visual-only" home inspection). An annual inspection of the home's electrical is also recommended for aged homes.
Neutrals - Sharing Terminal
Grounded "neutral" conductors were sharing a terminal with another neutral and/or ground wire(s) (EGC's) on the terminal bar(s). When a neutral conductor is sharing a terminal with another neutral conductor, it can prevent a circuit from safely being isolated for repair. It can also create an overvoltage condition that may damage lighting and appliances during servicing of the panel and circuits.
Mixed neutrals and grounds at a terminal can potentially allow current to flow on a ground wire during servicing of a circuit, which can possibly create a shock hazard on metal appliances on one circuit, or an overcurrent situation on another circuit. While panel manufacturers will allow for up to three grounding conductors under a single lug, they typically only allow one neutral wire. The grounding conductors aren’t going to normally carry current for extended periods of time, so they have a very slim possibility of coming loose. This isn’t the case with the neutral conductors. All grounded neutral conductors in this panel are recommended to be isolated on a separate terminal on the terminal bar.
408.41 Grounded Conductor Terminations. Each grounded conductor shall terminate within the panel board in an individual terminal that is not also used for another conductor. Exception: Grounded conductors of circuits with parallel conductors shall be permitted to terminate in a single terminal if the terminal is identified for connection of more than one conductor.
Knob and Tube: Information
SFTY - "Knob and tube" wiring was present in the home, and this wiring does not typically provide enough power for modern needs – which can result in a dangerous over-stressing of the electrical system, which could lead to a fire. Over time, the wire's insulation becomes brittle and deteriorates, resulting in exposed conductors and a risk of shock and/or fire. This wiring can be a potential fire hazard by covering it with insulation (a common practice) and incorrectly tapping new wiring into it. It is not within the scope of this inspection to determine what percentage of this property's wiring is "knob and tube" or to determine what percentage of the knob and tube wiring is energized vs. abandoned, as I can not tell what is behind the wall and ceiling coverings. A full evaluation of the knob and tube wiring is recommended with repairs and/or replacement made as deemed necessary for safety. I also recommend consulting with your Insurance company as some insurance companies may deny coverage due to knob and tube wiring.
*For more information regarding knob & tube wiring, please see the InterNACHI article titled, 'Knob-and-Tube Wiring'.


Wiring - Braided Cloth NM Present
AGED - There was braided cloth NM wiring in this home. This is the predecessor for today's polyvinyl chloride (Romex-like) wiring. This wiring's insulating jacket, both external and the individual jackets covering the conductors themselves, becomes brittle with age and can be damaged easily, particularly at securement points to studs and joists, in hot attics, and at bend points in the wiring. Typically this form of wiring does not contain an EGC (ground wire). Upgrading this wiring is recommended to be considered due to its age alone. For safety, AFCI breakers are recommended to protect the circuits with braided cloth NM wiring, as the breaker would trip if a damaged section of the wiring were to arc. I also recommend that any electrical conductors over 40 years of age be evaluated by a licensed electrician to ensure they are performing safely and as intended. For additional understanding please click HERE to view a great document by the Casualty Underwriters Association of America.
FYI: Braided cloth was usually used in homes that were built before 1960, and it was very common because it was inexpensive, and this rubberized-cloth was the standard method of insulating wires before plastics became widespread and affordable.
Two-Prong Present
AGED/SFTY - There were outdated, ungrounded 2-prong receptacles present in the home. This can be common in homes built pre-1970s, this form of wiring has a hot and neutral conductor present, with no grounding protection (EGC). These receptacles will not protect appliances or electronics plugged into them utilizing a third grounding prong and can also be a shock hazard with appliances containing a metal housing or enclosure. I recommend consulting with a licensed electrician about upgrading to grounding protection or at a minimum, installing GFCI protection for these receptacles/circuits coupled with a whole home surge protector.
*For further understanding, please watch the following videos regarding Two-Prong Electrical Receptacles:
1. How to Ground a Two-Prong Electrical Outlet | Ask This Old House
Open Ground (Older Wiring)
SFTY - There were three-prong receptacle(s) present that tested as being ungrounded. This indicates older wiring, with only hot and neutral wires present. This is due to a 2-prong receptacle being replaced with a 3-prong receptacle without the replacement of the branch wiring. This is not standard practice, as the receptacle should have been replaced with another 2-prong receptacle or protected by a GFCI-protected receptacle or breaker. The receptacles would then need to be designated as "No equipment ground" and "GFCI Protected."
There are situations with metal-housed appliances utilizing a third grounding prong (washing machines, toasters, etc.), where this could be a shock hazard, with loss of the neutral. As well, any electronic equipment utilizing a third grounding prong (TVs PCs, etc.) will not be protected from power surges or lightning strikes without the installation of a whole home surge protector installed at the electrical panel. An evaluation of the receptacles in the home is recommended with repairs made as needed for safety and the protection of electrical appliances.
FYI: Ungrounded three-prong outlets are a very common defect found during inspections of older houses. Thankfully, repairing this issue is not a huge deal, and the following blog explains different repair options. This is not a DIY guide for handy homeowners, and should only be performed by a licensed electrician. Blog: 'Options for repairing ungrounded three-prong outlets'.
Open Ground (GFCI Protected)
There were receptacle(s) present in the referenced area(s) that were ungrounded but were protected by GFCI protection. This is considered an acceptable "repair" for ungrounded receptacles as it will protect you from a safety standpoint by tripping if a fault occurs. But, this "repair" will not protect appliances and electronics utilizing a third grounding prong from power surges and lightning strikes, as a whole-home surge protector installed at the electrical panel would be needed. The actual GFCI receptacles should be designated with a sticker stating "No Equipment Ground", and each receptacle protected downstream should be designated with two stickers; one stating "GFCI Protected", and the other stating "No Equipment Ground". An evaluation of this "repair" is recommended to be performed to confirm all ungrounded receptacles are protected, that proper designation has been added, and to learn more about whole-home surge protectors.
Open Neutral
An electrical tester indicated that the receptacle has an open neutral. In order to prevent a shock hazard or a potential fire hazard, I recommend having this evaluated.
FYI: An open neutral occurs when the neutral wire has a loose connection between two points. Electrical current flows through the hot wire to receptacles, lights, and appliances. The neutral wire completes the circuit path back to the electrical panel. An open neutral disconnects or is loose, causing lights to flicker or appliances to operate inconsistently.
Open neutral means the white wire (neutral) in a 120-volt circuit in your house is broken. If the neutral breaks, the circuit is incomplete because no electricity returns to the panel.
Interior Unit (Gas) - Aged
The key to all combustion equipment is the heat exchanger. This is a welded clam-shell piece of metal inside of the furnace that contains the products of combustion so that moisture, carbon monoxide, and other products of combustion do not mix with interior air and get safely vented to the exterior. Heat exchangers on modern furnaces have an average life expectancy of 15-20 years. Unfortunately, heat exchangers are buried inside of heating equipment, are not visible, and are specifically excluded from a home inspection. The risk of continuing to use older gas equipment is the possibility of forming a crack in the heat exchanger and never being aware of it. I recommend that you have operable carbon monoxide alarms inside the house, have HVAC servicing performed annually, and anticipate replacing forced air furnaces on a roughly 15-20 year schedule.
To view CNHInspections life expectancy chart please click HERE.
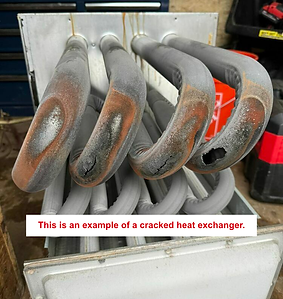
Lateral Load Devices - Missing
The deck was missing lateral load connectors. Lateral load connectors are recommended to be in place to provide resistance against lateral loads. While a well-fastened deck ledger is capable of resisting lateral forces, that connection can fail if the ledger or house rim board is compromised by rot. A dedicated lateral load connection transfers the loads from the deck frame to the frame of the house. It is recommended that lateral load connectors provide a total of at least 3000 pounds of lateral load resistance. An evaluation and repairs to incorporate lateral load devices is recommended. For an informational article please click HERE.

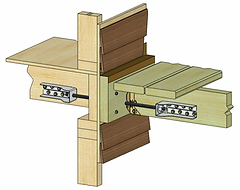

